1. Leakage of oil circuit board and check valve
Reason:
1. The casting quality of the cast iron parts is not high, and the oil circuit board and the single-flow valve body have shortcomings such as sand holes, loose mechanisms, and welding bumps;
2. It will crack in cold storage;
3. The welding of electric welding is not good, and there are shortcomings such as welding bumps, non-electric welding and internal stress cracks;
4. The pig iron valve is damaged after being hit by the hanging object.
Maintenance method:
1. Improve the casting quality, and carry out the compressive strength test in strict accordance with the regulations before installation;
2. For valves whose temperature is within 0°C and 0°C, thermal insulation or heat mixing should be carried out, and the valves that are deactivated should be cleared of stored water;
3. The welding of the oil circuit board and the one-flow valve combined by electric welding should be carried out according to the relevant electric welding safety operation rules, and the flaw detection and compressive strength test should also be carried out after welding.
4. It is strictly forbidden to push and place hanging objects on the valve, and it is not allowed to use a hammer to collide with the valve of pig iron and non-metallic materials. The installation of large-diameter valves should have a support frame.
2. Leakage at the packing
The exposure of the valve, the proportion of the packing is relatively large.
Reason:
1. The packing is not used correctly, it is not resistant to corrosion of substances, and it is not resistant to valve high pressure or vacuum pump, high temperature or ultra-low temperature application;
2. The packing is installed incorrectly, and there are shortcomings such as replacing the big with the small, the spiral winding connection is not good, and the tightening is loosening;
3. The filler exceeds the service life, has aged, and lacks ductility;
4. The precision of the valve stem is not high, and there are disadvantages such as bending, corrosion and damage;
5. The number of packing circles is not enough, and the gland is not clamped tightly;
6. The gland, anchor bolts, and other components are damaged, so that the gland cannot be clamped;
7. The actual operation is unreasonable, excessive force, etc.;
8. The gland is inclined, and the gap between the gland and the valve stem is too small or too large, resulting in damage to the valve stem and damage to the packing.
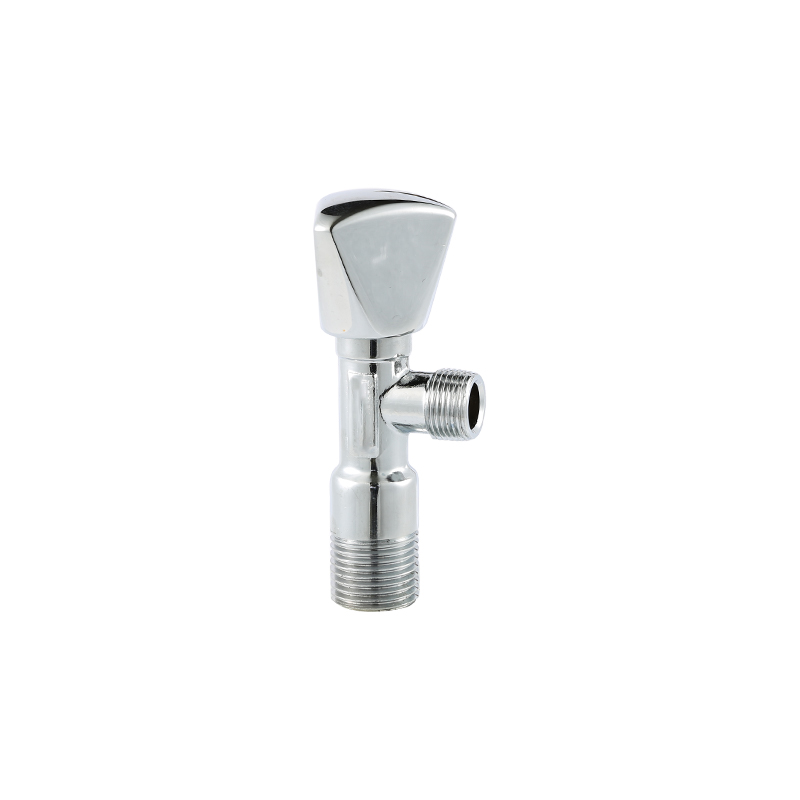
Maintenance method:
1. The raw materials and forms of fillers should be used according to the working conditions;
2. The packing should be properly installed according to the relevant requirements, the packing should be placed and clamped one by one, and the connecting head should be at 30°C or 45°C;
3. The packing with too long service life, aging and damage should be replaced immediately;
4. After the valve stem is bent or damaged, it should be straightened and repaired. If the damage is more serious, it should be replaced immediately;
5. The packing should be installed according to the specified number of turns, the gland should be tightened symmetrically and evenly, and the pressure sleeve should have a torque gap of more than 5mm;
6. Damaged glands, anchor bolts and other components should be repaired or replaced immediately;
7. The safety operation Zinc handle, hand polish and chrome procedures should be followed. Except for the collision-type spindle, the actual operation should be performed with normal energy at an average speed;
8. Tighten the gland bolts evenly and symmetrically. If the gap between the gland and the valve stem is too small, expand the gap as much as possible; if the gap between the gland and the valve stem is too large, it should be replaced.
3. Leakage of the convex surface
Reason:
1. The grinding of the raised surface is uneven, and the tight line cannot be produced;
2. The top center of the junction of the valve stem and the shut-off part is suspended in the air, skewed or damaged;
3. The valve stem is bent or the installation is skewed, so that the shut-off piece is inclined or missed;
4. The quality of the raised surface material is unreasonable or the valve is not adopted according to the working condition standard.
Maintenance method:
1. Appropriately use the raw materials and forms of the washers according to the working conditions;
2. Adjust carefully and stabilize the actual operation;
3. The anchor bolts should be screwed evenly and symmetrically, and a torque wrench should be used when necessary. The pre-tightening force should meet the regulations and should not be too large or small. There should be a certain torque gap between the flange and the flange connection;
4. The washer installation should be aligned at the center, the bearing force is even, the washer is not allowed to overlap the steel bars and use double washers;
5. If the static protruding surface is eroded, damaged in production and processing, and the processing quality is not high, maintenance, grinding, and coloring inspection should be carried out to make the static protruding surface meet the relevant regulations;
6. When installing the gasket, pay attention to cleaning, use gasoline to clean the raised surface, and the gasket cannot be floor-mounted.
4. Leakage at the connection between the sealing rings
Reason:
1. The sealing ring is not rolled tightly;
2. The sealing ring is welded with itself by electric welding, and the quality of spray welding is poor;
3. The outer thread, screw and pressure ring of the sealing ring are loose;
4. The sealing ring is connected and corroded.
Maintenance method:
1. The leakage at the sealing rolling place should be injected with adhesive and then rolled to fix it;
2. The sealing ring should be repaired by welding again according to the welding standard. When the spray welding place cannot be repaired by welding, the original spray welding and production processing shall be carried out;
3. Remove the screws, clean the pressure ring, dismantle and replace the damaged components, grind the sealing surface and the contact surface of the connecting seat, and reassemble. For components with relatively large erosion damage, it can be repaired by electric welding, bonding, etc.;
4. The connecting surface of the sealing ring is corroded, and it can be repaired by grinding, bonding, etc. If it cannot be repaired, the sealing ring should be replaced.
5. The switch-off piece falls off and causes leakage
Reason:
1. The actual operation is not good, so that the switch-off piece is stuck or exceeds the top dead center, and the junction is damaged and broken;
2. The connection of the switch-off is not strong, and it falls off due to loosening;
3. The material of the connector is incorrect, and it cannot withstand the corrosion of the material and the damage of the mechanical equipment.
Maintenance method:
1. Proper operation, close the valve can not be too hard, open the valve can not be higher than the top dead center, after the valve is fully opened, the spindle should be reversed a little;
2. The connection between the shut-off piece and the valve stem should be firm, and there should be a stopper at the flange connection;
3. The standard parts used for the connection between the shut-off part and the valve stem should withstand the erosion of substances, and have certain impact toughness and wear resistance.